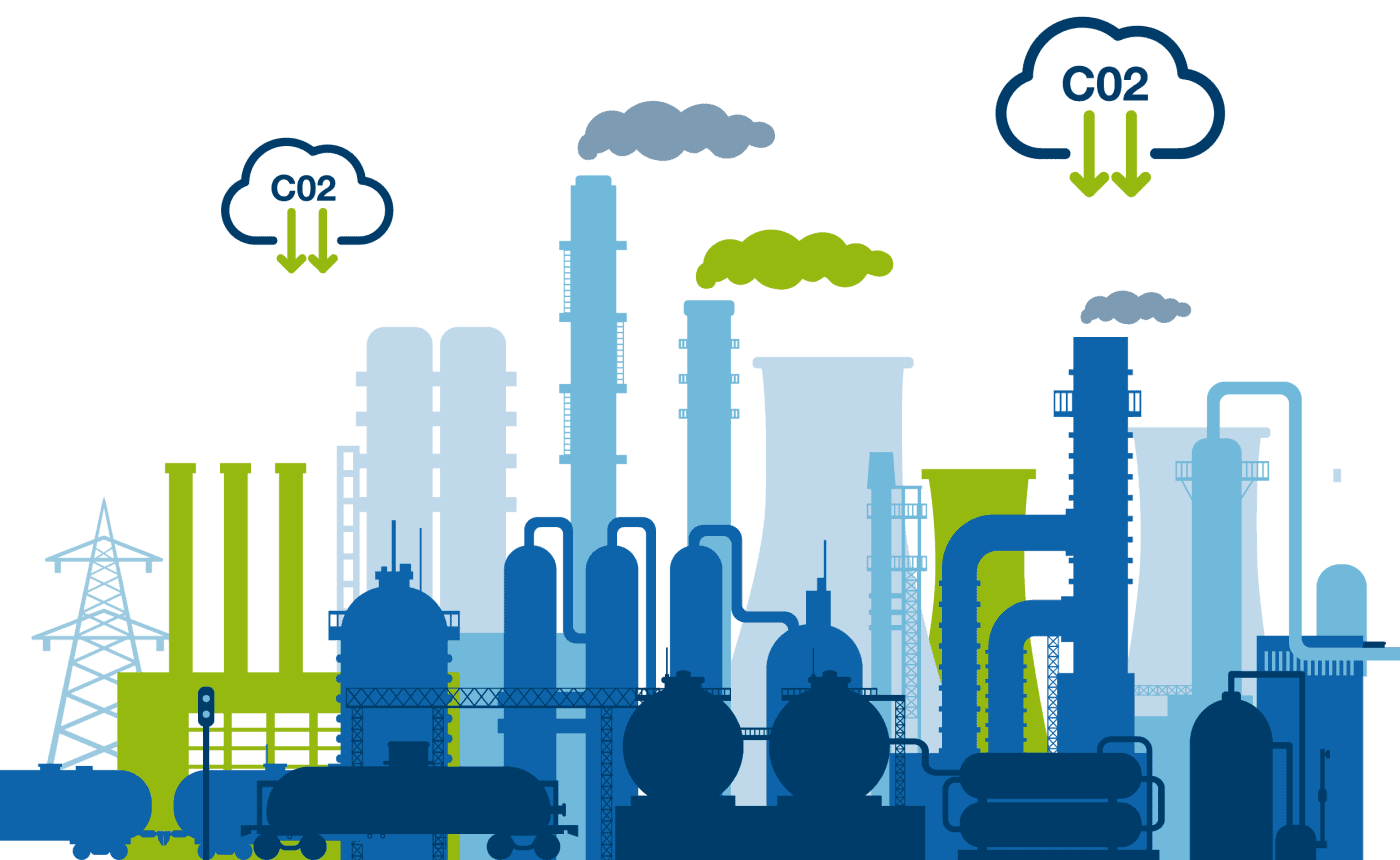
ECO SEAL – Low Emissions Spiral Wound Gasket
Here at KLINGER our standard spiral wound gasket exceeds all existing specifications and corresponding leakage requirements. Now, we have gone further and engineered a spiral wound gasket that is up to 10x tighter than our regular spiral wound gaskets. The KLINGER ECO-SEAL gasket has been manufactured in accordance to ASME B16.20-2017 and requires minimal alternations to your specification whilst reducing your plants fugitive emissions.
The concept behind Eco-Seal is not just a tighter gasket, its being able to quantify a reduction in plant emissions. Whilst other manufacturers may look to promote leakage rates of their spiral wound gaskets through gasket industry tests such as EN13555, KLINGER UK are going further. We can provide you with data that you can understand and can relate to. When in combination with KLINGER INTEGRITY SERVICES, we can offer you the complete emissions reduction program from gasket, installation, testing and recording.
Features:
- High density construction resulting in increased mechanical stability.
- Modified winding strip form
- High quality graphite filler
- Controlled filler protrusion
- Improved leakage performance at lower stresses
For even the most demanding applications:
- Hydrocarbon
- Steam
- Chemical
- Petrochemical
- Power

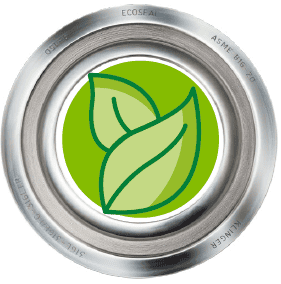
Overview of types ECO SEAL – Low Emissions Spiral Wound Gasket
Construction
- 316SS outer ring
- 316SS inner ring
- 316SS winding strip
- High purity graphite filler
Standards
- ASME B16.20-2017
- Fire Safe to API 6FB
- NACE MR0175
Gasket Factors
- M 3
- Y 10,000 PSI